Optimizing the geometry and profile of wear-resistant guide rails is crucial for enhancing their load distribution, wear resistance, and overall performance in industrial applications. Here are several ways the design elements can be adjusted to improve these factors:
Profile Shape
Curved or Contoured Profiles:
A curved or contoured profile can help distribute the load more evenly across the surface of the rail. This reduces localized stress points, preventing wear and improving the longevity of the guide rail. For example, a radius or arc-shaped profile ensures that the contact area is spread over a broader surface, reducing the pressure at any single point.
V-shaped or U-shaped Grooves:
Grooves or channels in the rail profile, such as V-shaped or U-shaped grooves, can help direct the load along specific paths, distributing the force more efficiently. These designs also enhance the stability of moving parts and allow for better integration with rail-mounted components (like carriages or sliders).
Contact Surface Area
Wider Contact Areas:
By increasing the width of the rail’s contact surface, the load is spread across a larger area, which helps distribute forces more uniformly. A wider profile reduces the risk of excessive wear on any single part of the rail, extending its service life. This is particularly important in heavy-duty applications where large forces are at play.
Multiple Contact Points:
Incorporating multiple contact points along the rail (e.g., through multi-track systems or overlapping contact surfaces) can help evenly distribute the load. This design spreads the stress across several points of contact instead of relying on just one, which can prevent premature failure of the rail.
Load-Bearing Surface Material
Material Selection for Load Distribution:
The choice of material and its properties play a key role in load distribution. Harder materials (like high-carbon steel, alloys, or coated materials) resist deformation under heavy loads, while softer materials may be better suited for applications with lighter loads or where shock absorption is important. The material should be optimized not only for wear resistance but also for the specific load conditions of the application.
Rail Height and Thickness
Increased Rail Height:
Increasing the height of the rail can enhance its ability to handle vertical loads, as it allows the rail to better absorb forces acting in the vertical direction. This is particularly useful in elevated or multi-axis applications where forces are applied from multiple directions.
Optimizing Thickness for Strength and Flexibility:
The thickness of the rail should be optimized to balance strength with flexibility. A thicker rail can handle higher loads, but if it’s too thick, it may cause material fatigue or over-stress in localized areas. The ideal thickness ensures both strength and the ability to flex slightly under load without warping or failing.
Tapered Edges or Ramps
Tapered Rails:
Introducing tapered edges or ramp-like features on the rail profile can help transition loads more smoothly. Tapered profiles allow for gradual load distribution rather than a sudden concentration of force at specific points, which helps prevent wear and tear on both the rail and any moving components that interact with it.
Chamfered Edges:
Chamfering or rounding the edges of the guide rail reduces stress concentrations, particularly where the rail is in contact with moving parts. This helps prevent localized wear and damage to both the rail and the guide system.
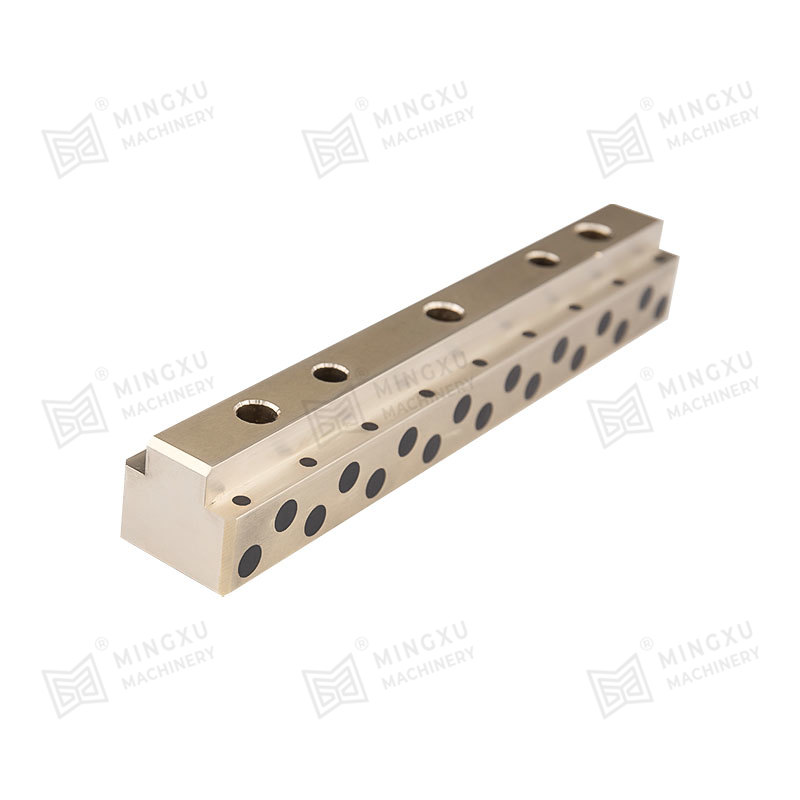
Cross-Sectional Design
I-beam or Box Section:
Using an I-beam or box-shaped cross-section provides a high level of rigidity and strength while optimizing material usage. These designs are particularly effective for handling high loads because they increase the moment of inertia, providing better load distribution along the length of the rail. The hollow section of an I-beam or box design also reduces weight without sacrificing strength.
Integration of Reinforcements
Internal Reinforcements:
Adding internal reinforcements, such as steel inserts or reinforced ribs, within the rail structure can increase its ability to handle loads without deformation. These reinforcements enhance the rail's ability to distribute loads evenly, especially in areas subject to high stress or potential bending.
Segmented Rail Design
Modular or Segmented Rails:
A segmented rail design breaks the rail into smaller, modular sections, allowing the guide rail to be more adaptable and better at distributing loads across different points. These smaller sections can be individually optimized for specific load types and conditions, allowing for better overall performance in complex systems.
Load Distribution Along the Length of the Rail
Gradual Tapered Profiles Along the Length:
Rails can be designed with a gradual taper along their length, allowing for more efficient load distribution at different points. This method can improve overall stress management across the entire length of the rail, reducing the risk of localized failure due to high load concentrations.
Use of Dynamic Load Distribution
Active Load Distribution Systems:
In some advanced applications, dynamic load distribution systems can be incorporated, where sensors or feedback systems monitor the load and adjust the rail geometry or lubrication automatically to optimize the load distribution. This is typically used in highly dynamic environments where loads change frequently.
Customization for Specific Application Needs
Tailored Geometries for Specific Loads:
Depending on the application (e.g., conveyor systems, robotics, or precision machinery), the geometry can be customized to handle specific types of load forces (e.g., linear, rotational, or shock loads). For instance, rail designs for robotic arms often feature customized profile angles and high-tolerance grooves to ensure both precise movement and efficient load distribution.
Contact Us