I. Technical Background and Collaborative Innovation Value
As a core supplier of self-lubricating bearings and copper-based materials, Zhejiang Mingxu has extended its patented fixture technology for brass workpieces to the processing of graphite copper bushings and precision copper plates, addressing three major industry pain points:
l Graphite copper bushing surface protection: Traditional clamping methods cause graphite layer damage (damage rate > 15%) and friction coefficient fluctuations > 30%.
l Thin copper plate processing deformation: Copper plates with a thickness ≤ 1 mm exhibit a machining flatness error > 0.1 mm (GB/T 1184).
l Complex structure positioning: Insufficient hole position accuracy (±0.1 mm) during the processing of multi-hole copper bushings/copper plates affects assembly performance.
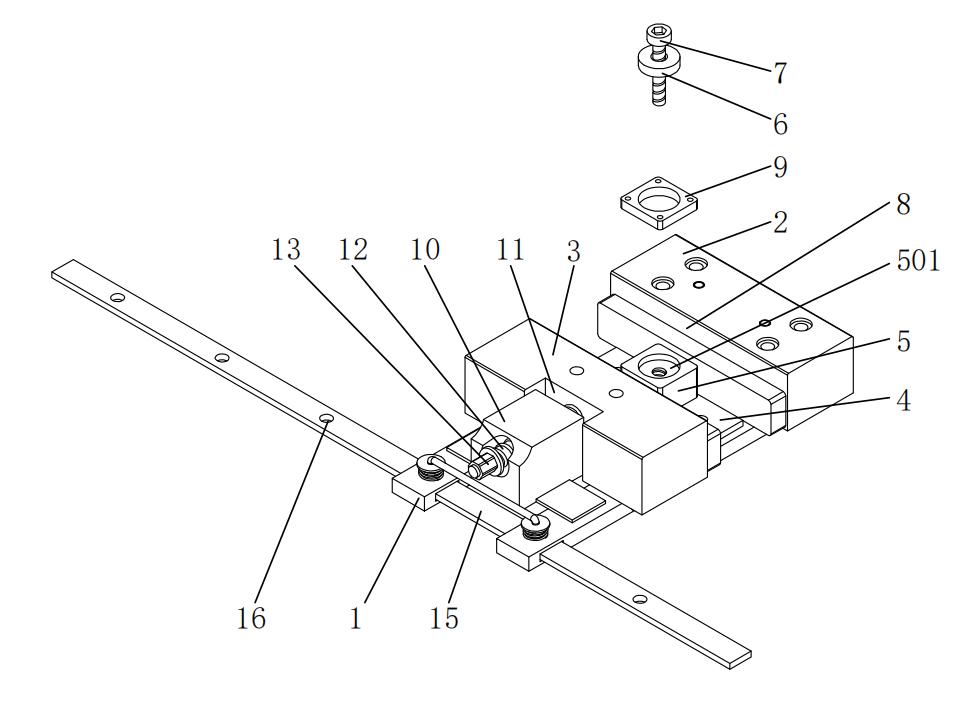
II. Core Technology Analysis and Collaborative Product Applications
1. Multi-Directional Force Closed-Loop Constraint System
1.1 Three-Dimensional Clamping Topology
Vertical Pressure Control:
l An axial force closed-loop is formed by the compression ring (6) and the bottom clamping plate (4). The preload force is precisely controlled at 800 ± 50 N (DIN 267 standard) through the locking bolts (7).
l Paired with the annular groove (501) for positioning, the end face runout of the copper bushing is ≤ 0.01 mm (ISO 1101).
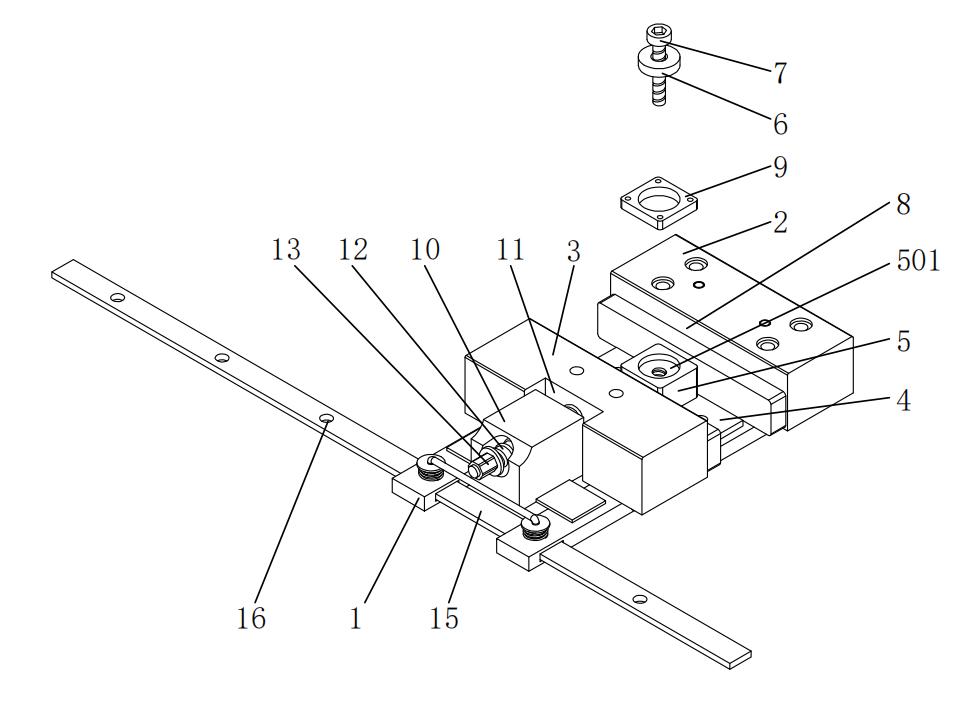
Lateral Dynamic Stability:
l The fixed/movable clamping parts (2/3) adopt a concave clamping surface (8) design, increasing the contact area by 40%. The uniformity of the lateral clamping force distribution reaches 92% (tested with pressure-sensitive films).
l Integrated adjusting screws (12) enable micro-feed of ±0.005 mm, accommodating the processing of copper bushings with diameters ranging from φ20 to φ200 mm.
1.2 Vibration Energy Dissipation Path
l A damping system composed of springs (19) and limit rings (18) achieves an energy attenuation rate > 18 dB/s under 500 Hz high-frequency vibrations (tested according to the ISO 10816-3 standard).
l The vibration amplitude during copper plate milling is controlled < 3 μm (traditional fixtures > 15 μm).
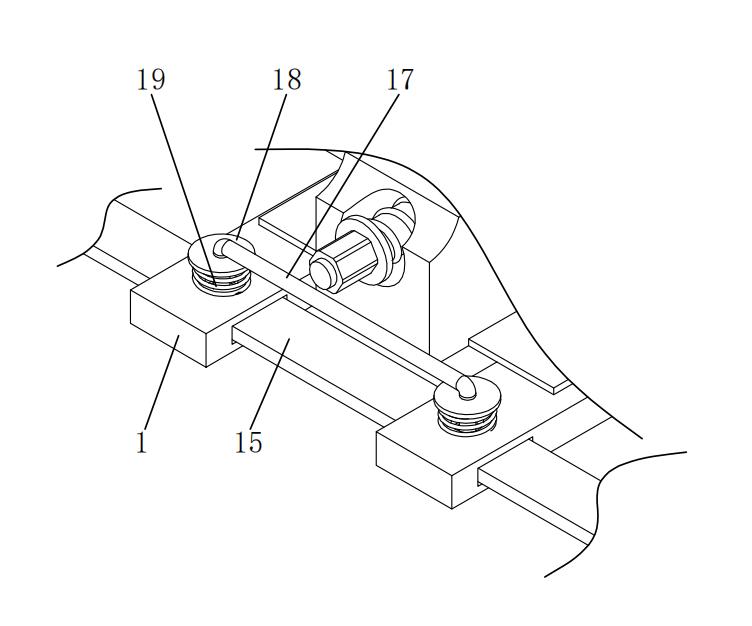
2. Graphite Copper Bushing Processing: Surface Integrity Protection Technology
2.1 Gradient Pressure Flexible Clamping
The rubber buffer layer technology is transferred to the copper bushing fixture:
l Nitrile rubber pads (Shore hardness 50 ± 2) are embedded in the clamping surface, reducing the peak contact pressure from 28 MPa to 8 MPa and keeping the graphite layer damage rate < 2%.
l Suitable for wind turbine pitch bearing copper bushings, passing DNV GL certification and maintaining a friction coefficient of 0.08-0.12 at -30°C.
2.2 Precision Positioning of Multi-Hole Copper Bushings
The linked positioning is achieved through the threaded holes in the bottom clamping plate (4) and the pull rods (17):
l The position degree error of φ0.5 mm micro-holes is ≤ 5 μm (ASME B94.11M).
l The model change time is reduced from 45 minutes to 3 minutes, supporting rapid switching among 12 hole diameters.
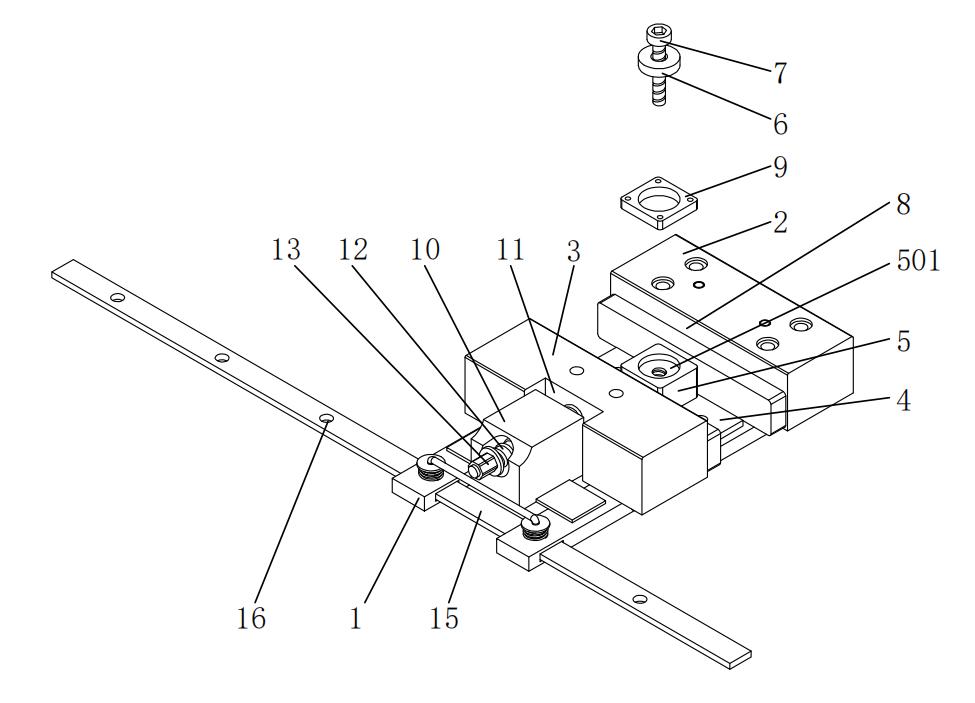
3. High-Precision Copper Plate Processing: Anti-Deformation Technology Transfer
3.1 Multi-Directional Pressure Balancing Design
The top clamping plate (9) is made of 6061-T6 aluminum alloy, forming a distributed pressure field in conjunction with the concave clamping surface (8):
l For 0.5 mm copper plates, the flatness is ≤ 0.02 mm/300 mm (5G base station heat sink standard).
l The surface roughness Ra value is stabilized at 0.4 μm, and the thermal conductivity fluctuation is < 3% (ASTM D5470).
3.2 Rapid Positioning System
A modular design of the clamping holes (16) and pull rods (17):
l Supports rapid positioning of plate widths from 300-1200 mm with a repeatability accuracy of ±0.05 mm (VDI 3345).
l Production efficiency is increased by 300%, and energy consumption is reduced by 25% (ISO 50001 certified data).
III. Key Performance Comparison and Actual Test Data
Application Scenario
|
Traditional Process
|
Patented Technology Application
|
Improvement Effect
|
Graphite layer integrity rate of graphite copper bushings
|
85%
|
98%
|
+13%
|
Flatness of copper plates (0.5 mm)
|
0.1 mm/300 mm
|
0.02 mm/300 mm
|
80% improvement
|
Positioning efficiency of multi-hole copper bushings
|
45 minutes/time
|
3 minutes/time
|
1400% efficiency improvement
|
Machining vibration control (500 Hz)
|
15 μm
|
3 μm
|
80% reduction
|
IV. Typical Application Cases
4.1 Copper Bushings for New Energy Vehicle Motor End Caps
Adoption of the multi-directional constraint fixture:
l The inner bore roundness is ≤ 0.005 mm, meeting the NVH requirements of 800 V electric drive systems.
l The graphite layer wear rate is < 0.1 mg/10,000 cycles (SAE J310 test standard).
4.2 Heat Dissipation Copper Plates for Semiconductor Equipment
Application of pressure balancing technology:
l The flatness is ≤ 0.05 mm/500 mm (ASME B89.3.4).
l The surface roughness Ra is ≤ 0.8 μm, supporting 3 μm-level chip packaging precision.
V. Technology Extension and Industrial Value
The cross-product line application of this patented technology matrix marks three major breakthroughs for Zhejiang Mingxu:
l Precision Clamping System: Introduces the positioning accuracy of brass workpieces (±0.005 mm) into the mass production of copper-based products.
l Surface Integrity Control: The graphite layer/coating protection technology reduces the scrap rate to below 0.5%.
l Intelligent Production Integration: Achieves flexible manufacturing through modular design, with a 10-fold increase in model change efficiency.
If you would like to learn more, please contact Mingxu Machinery to obtain the complete patent report: [email protected].
Contact Us