In precision machinery, industrial automation, and heavy-load transport systems, the guide rail plays a foundational role in maintaining directional stability, minimizing friction, and enabling smooth linear motion. However, when subjected to continuous stress, high speeds, and abrasive environments, conventional guide rails can suffer from rapid wear and performance degradation. This is where wear-resistant guide rails—engineered with advanced materials and surface treatments—become indispensable.
Far from being a passive structural component, the wear-resistant guide rail is a critical enabler of long-term reliability, dimensional accuracy, and maintenance efficiency across a spectrum of demanding applications. This article delves into the technical architecture, materials science, and applied engineering that make wear-resistant guide rails vital for high-performance machinery.
The Mechanical Purpose of a Guide Rail: Stability in Controlled Motion
At their core, guide rails are linear reference structures that constrain and direct the movement of associated components—carriages, sliders, bearings, or mechanical arms. They are designed to support both axial and radial loads while minimizing lateral deviation during motion. In automated production systems, CNC machines, robotic assembly lines, and transportation conveyors, guide rails must not only maintain positional accuracy but also endure continuous cycling under high loads.
When such systems operate at elevated speeds, in abrasive settings, or with minimal lubrication, standard steel rails may quickly degrade due to surface fatigue, fretting corrosion, or particulate-induced abrasion. This not only leads to increased maintenance intervals but also compromises the repeatability and accuracy essential in precision-driven environments.
Wear-resistant guide rails solve this problem by integrating advanced metallurgy, coatings, and structural enhancements to withstand prolonged mechanical stress while maintaining smooth operation.
Material Science Behind Wear Resistance
The durability of wear-resistant guide rails is fundamentally rooted in material selection and surface engineering. Several strategies are employed to significantly improve the life span of the rail under harsh operating conditions:
-
Alloy Steel Base Materials
High-carbon or alloy steels (e.g., AISI 52100, chrome-moly steels) serve as the foundation, offering superior hardness and fatigue resistance. These steels are often quenched and tempered to optimize the microstructure for enhanced wear performance.
-
Surface Hardening Techniques
Induction hardening, carburizing, and nitriding are applied to increase the hardness of the rail surface without compromising the toughness of the core. Such hardened layers typically reach surface hardness levels of HRC 58–65, allowing the rail to resist pitting and micro-cracking even under cyclic loads.
-
Wear-Resistant Coatings
Advanced coatings like hard chromium, ceramic, PVD (Physical Vapor Deposition) layers, or diamond-like carbon (DLC) further enhance surface wear resistance, reduce friction, and provide corrosion protection. In cleanroom or chemical environments, anti-stick and non-reactive coatings are particularly valuable.
-
Composite and Polymer-Embedded Designs
For environments involving dust, shock, or vibration, some wear-resistant guide rails incorporate self-lubricating polymer inlays or hybrid composites that absorb vibration while maintaining low-friction movement.
-
Surface Finish and Geometry Control
Ultra-fine grinding, honing, and lapping ensure a low Ra (roughness average), typically <0.4 µm, which helps reduce abrasive wear and noise during operation.
Performance Advantages in Demanding Applications
Wear-resistant guide rails are engineered to meet the needs of high-duty systems where standard rails would fail prematurely. The following performance advantages are key to their value proposition:
-
Extended Service Life
Through enhanced surface hardness and low-friction properties, these rails exhibit a significant increase in operating lifespan, even in continuous-use settings.
-
Reduced Maintenance and Downtime
The wear resistance translates directly to fewer replacements, less need for lubrication, and reduced machine downtime—especially critical in 24/7 manufacturing operations.
-
Dimensional Stability and Precision
Consistent rail dimensions and resistance to wear ensure that machine tools, automation systems, or inspection devices maintain micron-level accuracy over time.
-
Environmental Robustness
In environments exposed to dust, debris, corrosive agents, or temperature fluctuations, wear-resistant rails maintain performance integrity where standard options would degrade.
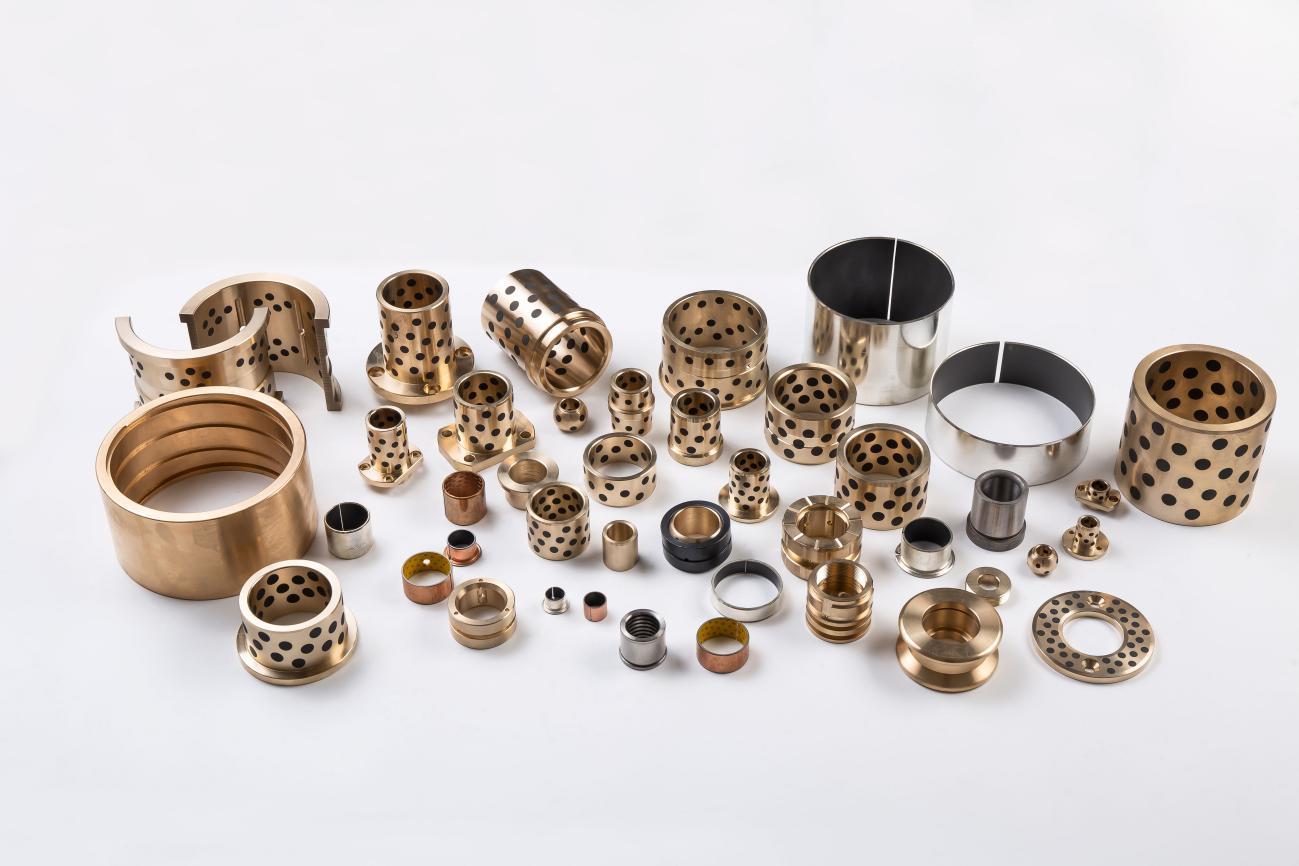
Industrial Applications Across Sectors
Wear-resistant guide rails are implemented in a wide variety of high-performance fields, including:
-
CNC Machining and Precision Tooling
Guide rails in CNC systems endure rapid back-and-forth motion under varying loads. Wear resistance ensures long-term positional accuracy, crucial for high-precision part production.
-
Automated Assembly Lines
In automotive and electronics manufacturing, conveyors and robotic systems rely on guide rails to position components accurately across multiple production stages.
-
Medical and Laboratory Equipment
Laboratory automation systems, such as sample analyzers and robotic pipetting units, demand ultra-smooth, wear-free motion for accurate and repeatable operations.
-
Heavy Equipment and Mining Machinery
In extreme load-bearing contexts, such as underground drills and material handling arms, wear-resistant rails help manage shock loading and abrasive debris.
-
Aerospace and Defense Systems
Actuation systems in aircraft or defense equipment benefit from the weight-to-performance ratio offered by specially engineered wear-resistant rails, where failure is not an option.
Future Development Trends and Smart Integration
As industrial systems become increasingly digitized and autonomous, the next generation of wear-resistant guide rails is evolving beyond passive components:
-
Integrated Sensing Technology
Rails embedded with wear sensors or strain gauges can monitor surface degradation in real time, allowing for predictive maintenance and improved system reliability.
-
Additive Manufacturing and Surface Texturing
Advanced 3D printing techniques may allow for custom surface textures that optimize lubrication retention or reduce dynamic friction in specific motion profiles.
-
Green Manufacturing and Sustainability
Development of eco-friendly coatings and recyclable rail materials will play a role in reducing the environmental footprint of heavy-duty automation systems.
Contact Us