Wound bushings, as critical self lubricating bushing components in mechanical systems, are widely used in bearings, gears, hydraulic cylinders, and other applications where friction and wear reduction are essential. Their unique split structural design not only addresses the limitations of traditional seamless bushings in installation and elastic adaptability but also significantly enhances the practicality, reliability, and cost-effectiveness of the components.
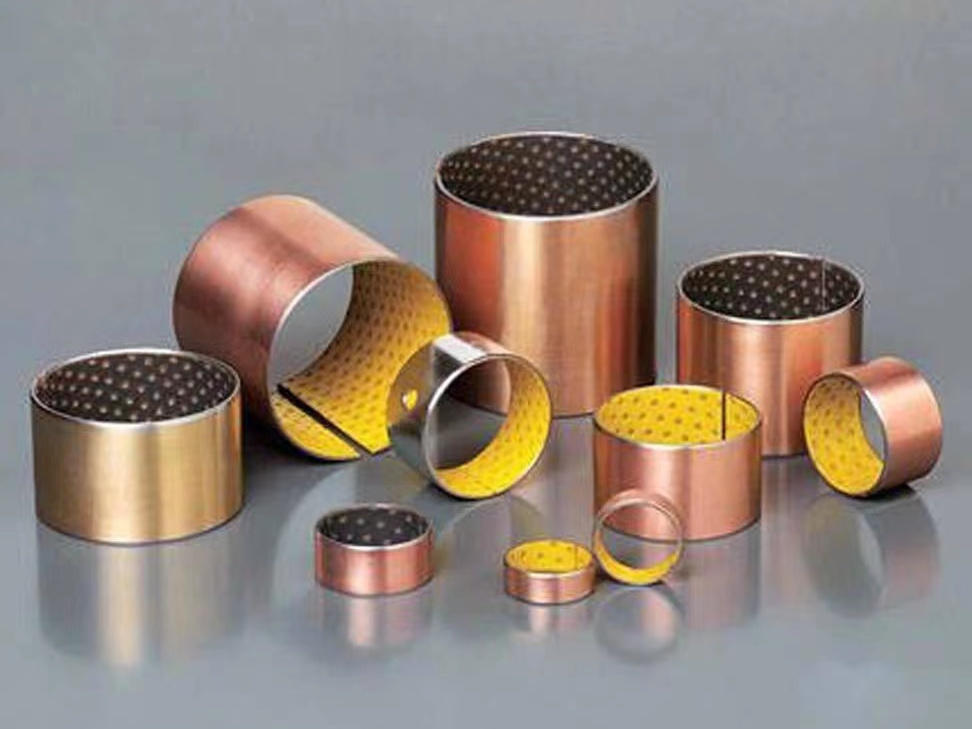
Facilitating Installation and Disassembly: Simplifying Processes and Reducing Precision Requirements
Wound bushings are split in their free state, allowing them to be easily pressed or installed onto shafts or into holes, with the seam closing to form a complete ring after installation. For example, in hydraulic cylinder assembly, split bushings are secured onto pipes through crimping, eliminating the need for complex tools or high-precision alignment and significantly reducing installation time. A mechanical engineering manufacturer's actual test data shows that using split bushings increased installation efficiency by 40% per piece and reduced scrap rates by 35%.
Adapting to Deformation and Elasticity: Enhancing Sealing and Impact Resistance
The split design enables the bushing to accommodate minor deformations in the shaft or hole during installation, providing superior sealing and fit. Additionally, the elastic structure absorbs vibrations and impacts, extending equipment lifespan. A case study of rubber bushings in automotive stabilizer bars demonstrates that the split structure distributes radial deformation evenly, improving vehicle handling stability by 20% and ride comfort by 15%.
Preventing Thermal Expansion Damage: Reserving Space to Avoid Cracking and Deformation
In high-temperature environments, the split structure provides space for thermal expansion, preventing the bushing from cracking due to heat. A chemical equipment manufacturer's test shows that pipes with split bushings operated continuously for 1,000 hours at 200°C without bushing damage, whereas traditional seamless bushings cracked after 500 hours under the same conditions.
Improving Processing Efficiency and Reducing Costs: Optimizing Processes for Better Economics
The split structure simplifies processing steps such as winding and shaping. Statistics indicate that material utilization rates on split bushing production lines are 12% higher than those for seamless bushings, and per-piece processing costs are reduced by 25%. Furthermore, the split design reduces waste generation, aligning with green manufacturing trends.
Facilitating Maintenance and Replacement: Quick Replacement to Minimize Downtime
Worn split bushings can be quickly removed and replaced, reducing downtime. A steel mill's hydraulic equipment maintenance records show that using split bushings reduced single maintenance times from 4 hours to 1.5 hours, increasing equipment availability by 30%.
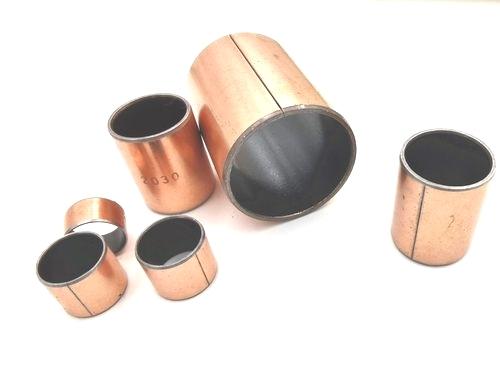
The split structural design of wound bushings is a product of the deep integration of materials science, process technology, and practical application requirements. Its five core advantages not only enhance component performance but also drive the entire mechanical system toward greater efficiency, reliability, and cost-effectiveness. In the future, with material innovations and process upgrades, the application scope of split bushings will further expand, providing more innovative solutions for the high-end equipment manufacturing industry.
Zhejiang Mingxu Machinery Manufacturing Co., Ltd. has specialized in producing self-lubricating bearings for over a decade. Wound bushings (such as SF-1, SF-2) are one of the company's mainstream products, highly favored and recognized by customers, and have stood the test of the market. If you have procurement needs, please contact us at: [email protected].
Contact Us