In modern industrial equipment, solid-embedded self-lubricating bearings are like the "silent guardians" of mechanical systems. Their performance directly determines the reliability, efficiency and life of equipment operation. As equipment manufacturing expands to extreme working conditions (such as deep sea, deep space, high temperature and high pressure), the traditional solution that relies on external grease lubrication has exposed obvious shortcomings - lubricants are easy to lose, pollute sensitive environments, and high maintenance costs. According to statistics, about 30% of industrial equipment failures are related to lubrication failures, and premature wear of bearings caused by incorrect lubricant selection can cause millions of economic losses each year.
The selection of solid lubricants is by no means a simple "material replacement", but a systematic project that requires the integration of materials science, tribology and working condition analysis. For example, in polar scientific research equipment at -50°C, ordinary lubricants may fail due to low-temperature embrittlement; and in vacuum satellite attitude control mechanisms, the degassing characteristics of lubricants may even threaten the safety of the entire satellite. These extreme cases highlight the necessity of scientific selection - not only to understand the physical and chemical properties of lubricants, but also to accurately match dynamic working parameters such as load, speed, temperature, and medium.
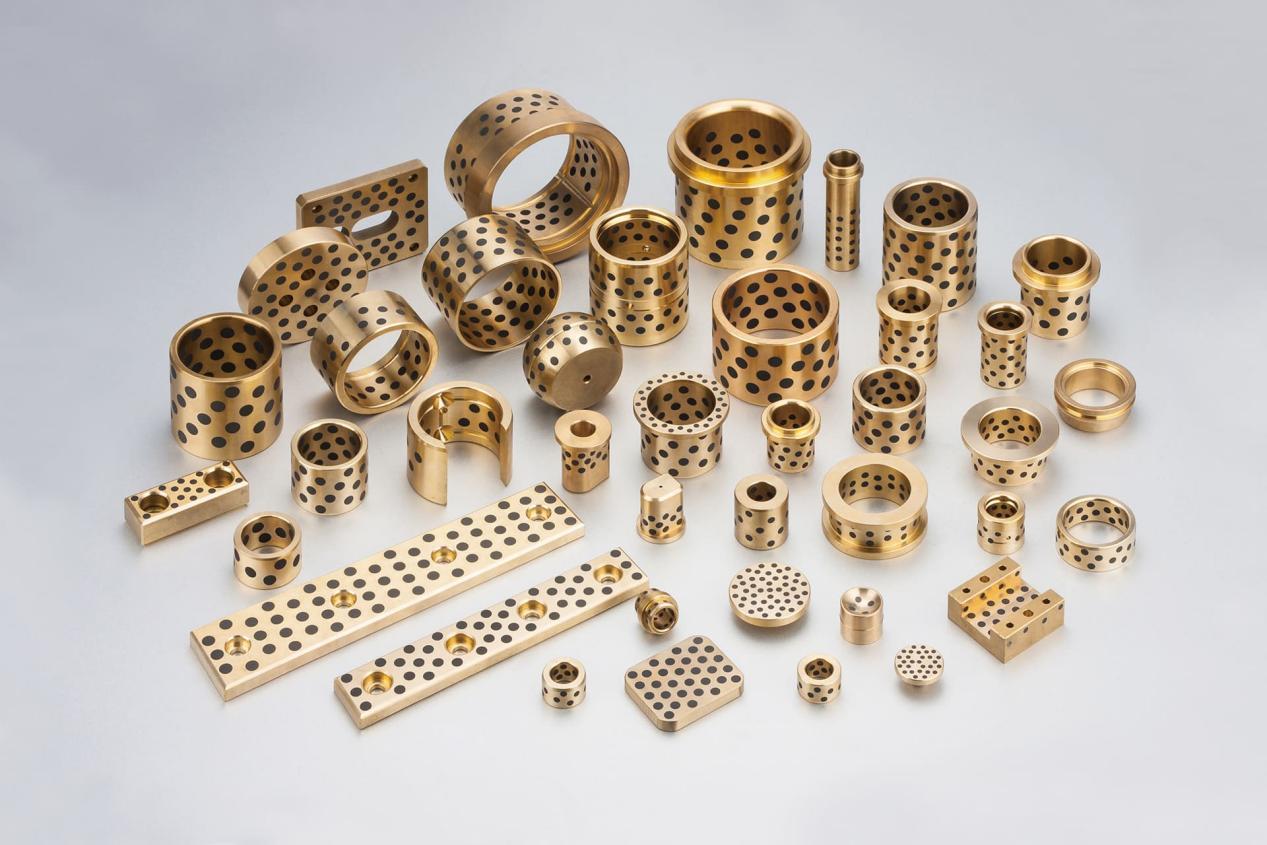
This article will systematically analyze the selection logic of solid lubricants through six core dimensions (temperature, load, environment, motion characteristics, material compatibility, and special needs), combined with real application scenarios in aerospace, new energy, heavy industry, and other fields. Whether facing rolling mill bearings in high-temperature steel mills or precision joints of medical robots, readers can get a "one-dose-one-policy" solution from it, realizing the leap from experience decision-making to data-driven.
1. Working temperature range
The temperature resistance of lubricants directly affects their lubrication effect and stability.
High temperature environment (>300℃): Choose graphite or molybdenum disulfide (MoS₂).
Example: Roller bearings in metallurgical equipment can operate at temperatures above 400℃. The layered structure of graphite can still form a continuous lubricating film at high temperatures to avoid direct metal contact.
Medium and low temperature environment (-50℃~200℃): Polytetrafluoroethylene (PTFE) or polymer composite materials are suitable.
Example: Conveyor belt bearings of food processing machinery, PTFE has a low friction coefficient (0.04~0.1) in the range of room temperature to 150℃, and meets food safety standards.
2. Load conditions
High load conditions require lubricants to have compressive strength and anti-extrusion capabilities.
Heavy load and low speed (>50MPa): Graphite or MoS₂is preferred.
Example: The support bearings of mining machinery withstand pressures above 80MPa, and the laminar shear characteristics of MoS₂can effectively disperse the pressure and prevent the lubrication film from rupture.
Impact load: It is necessary to match a high-toughness matrix (such as copper alloy) and use a graphite/MoS₂composite lubricant.
Example: Stamping machine guide column bearings, composite lubricants can buffer instantaneous impacts and reduce micro-motion wear.
3. Environmental media
Corrosive, humid or vacuum environments require targeted lubricant selection.
Wet/water environment: avoid using MoS₂(easily hydrolyzed to generate H2SO₄), use PTFE or boron nitride (BN) instead.
Example: Ship steering gear bearings are in contact with seawater for a long time, and the hydrophobicity and salt spray corrosion resistance of PTFE can extend the service life by more than 3 times.
Vacuum environment: graphite is prohibited (lubricity decreases after adsorbing gas), and MoS₂is selected.
Example: The bearings of the spacecraft deployment mechanism, the friction coefficient of MoS₂in vacuum (0.03~0.06) is lower than that in the atmosphere.
4. Movement speed
High-speed or low-speed movement has different requirements for the release rate of lubricants.
High speed (>2m/s): Use PTFE or graphite composite lubricants.
Example: The main shaft bearing of textile machinery has a speed of 10,000rpm. The low friction coefficient of PTFE can reduce heat and avoid bonding failure.
Low-speed reciprocating motion: MoS₂is more suitable because it can still form an effective transfer film under boundary lubrication conditions.
Example: Hydraulic cylinder guide sleeve, MoS₂ can reduce the wear rate to 0.001mm³/(N·m) at a low speed of 0.01m/s.
5. Compatibility and process adaptability
The lubricant needs to match the base material and manufacturing process.
Copper-based bearings: Graphite or MoS₂is preferred, and the temperature needs to be controlled during sintering (such as graphite sintering temperature <800℃).
Example: Automobile suspension bushings use copper-based + graphite, and the porosity of the lubricant is stable at 12%~15% after sintering to ensure continuous release.
Steel-based bearings: MoS₂+PTFE composite powder can be used to achieve high-strength bonding through cold pressing-sintering process.
Example: Heavy truck clutch release bearing, composite lubricant makes the base hardness reach HRC45 while maintaining lubricity.
6. Special industry requirements
Additional conditions such as environmental protection, hygiene or conductivity must be met.
Food/medical equipment: FDA-certified PTFE or ceramic-based lubricants must be used.
Example: Guide bearings of pharmaceutical filling machines, PTFE is non-toxic and resistant to chemical cleaning agents.
Conductive requirements: Choose graphite or metal-doped lubricants (such as silver-coated MoS₂).
Example: Electronic equipment cooling fan bearings, graphite can both lubricate and conduct static electricity to avoid circuit interference.
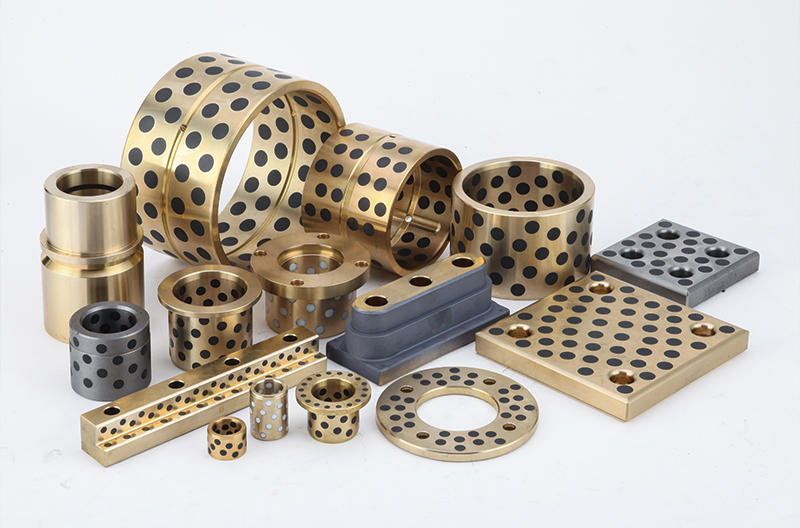
Summary: Prioritize the selection strategy
Identify extreme working conditions: Prioritize meeting the limit values of core parameters such as temperature and load.
Balance life and cost: For example, the aerospace field tends to prefer high-performance composite materials, while civil machinery may choose more cost-effective graphite.
Experimental verification: Quantify the actual effectiveness of lubricants through bench tests (such as ASTM D2714 friction and wear tests).
Through systematic analysis of working condition requirements, lubricants can be accurately matched to increase bearing life by 50%~300% while reducing maintenance costs. For example, after a wind turbine pitch bearing adopted the MoS₂+graphite composite lubrication solution, the maintenance cycle was extended from 6 months to 5 years in an environment with a temperature difference of -30℃~120℃ and salt spray corrosion
Contact Us