The shipping equipment is constantly subjected to seawater corrosion, high salt fog, heavy load impacts, and other challenges. As a core component of the power transmission and support system, self-lubricating bearings directly impact navigation safety and maintenance costs with their reliability. Traditional grease-lubricated bearings are prone to lubricant loss due to seal failure in marine environments, leading to seizing or wear. In contrast, insert-type self-lubricating bearings significantly reduce friction and maintenance requirements by continuously releasing a lubricating film through solid lubricants. However, the complex and diverse operating conditions of ships—ranging from intermittent impacts on deck machinery to continuous high loads on propulsion systems, and from extremely low temperatures in polar regions to high temperatures in engine rooms—require precise material selection.
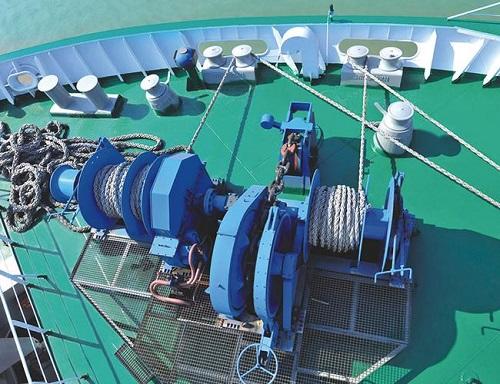
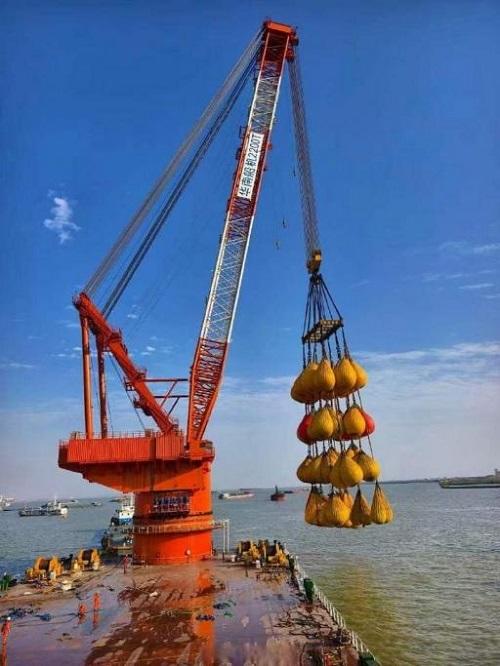
I. Characteristics of Ship Operating Conditions and Bearing Performance Requirements
Severe Environmental Challenges
Operating Condition
|
Typical Scenario
|
Bearing Performance Requirements
|
High Corrosivity
|
Seawater immersion, salt fog environment
|
Resistance to chloride ion corrosion, pitting resistance
|
Heavy Load and Impact
|
Anchor winches, rudder steering gear transmissions
|
High ultimate pressure (≥30 MPa), fatigue strength
|
Wide Temperature Range Fluctuations
|
Polar navigation (-30℃), engine room (60℃)
|
Low-temperature brittleness resistance, high-temperature strength retention
|
Vibration and Fretting Wear
|
Main engine supports, propeller shaft systems
|
High damping characteristics, fretting wear resistance (wear rate ≤1×10⁻⁴)
|
II. Comparison and Data Support for Ship Self-Lubricating Bearing Materials
1. Corrosion Resistance: A Core Threshold in Marine Environments
Material Type
|
Salt Spray Test (ASTM B117)
|
Seawater Immersion Corrosion Rate (mm/year)
|
Applicable Scenarios
|
High-Strength Brass
|
≥720 hours without red rust
|
0.02-0.05
|
Deck machinery, rudder bearings
|
Aluminum Bronze
|
≥1000 hours without red rust
|
0.01-0.03
|
Propeller shaft systems, seawater pumps
|
Stainless Steel-Based Composite
|
≥2000 hours without red rust
|
0.005-0.01
|
Submersibles, high value-added equipment
|
Tin Bronze
|
≤240 hours before dezincification
|
0.15-0.30 (accelerated dezincification)
|
Not recommended for marine environments
|
Key Conclusions:
l Aluminum bronze has the best salt spray resistance and is suitable for critical components in constant contact with seawater.
l High-strength brass offers good cost-effectiveness and meets the needs of most deck equipment.
l Stainless steel-based composites have excellent corrosion resistance but are 3-5 times more expensive than aluminum bronze and are only used in special ships.
2. Mechanical Properties: Heavy Load and Impact Resistance
Indicator
|
High-Strength Brass
|
Aluminum Bronze
|
Stainless Steel-Based Composite
|
Ultimate Pressure (MPa)
|
30-50
|
25-35
|
20-30
|
Fatigue Strength (MPa)
|
≥200
|
≥150
|
≥120
|
Impact Toughness (J/cm²)
|
80-100
|
60-80
|
40-60
|
Selection Recommendations:
l Anchor winches/capstans: Prioritize high-strength brass with an ultimate pressure of 50 MPa to handle instantaneous cable tensions (typically 35-45 MPa).
l Main engine support bearings: Aluminum bronze retains 85% of its strength at high temperatures (60℃ in engine rooms), outperforming high-strength brass (75%).
l Vibration damping brackets: Stainless steel-based composites have high damping performance (loss factor 0.05-0.08) but limited load-bearing capacity.
3. Lubrication and Wear: The Key to Maintenance-Free Operation
Material Type
|
Dry Friction
|
Coefficient Wear Rate (×10⁻⁴ mm³/(N·m))
|
Lubricant Release Lifetime (hours)
|
High-Strength Brass
|
0.08-0.12
|
0.5
|
8000-10000
|
Aluminum Bronze
|
0.10-0.18
|
1.2
|
6000-8000
|
Stainless Steel-Based Composite
|
0.05-0.10
|
0.3
|
12000-15000
|
Data Interpretation:
l Stainless steel-based composites have the lowest wear rate but are too expensive (about 120,000 RMB/ton) and are only used in submersible propeller bearings.
l High-strength brass has a lubrication lifespan of 10,000 hours (about 4 years of maintenance-free operation), meeting the 5-year docking repair cycle requirements of merchant ships.
l Aluminum bronze requires a graphite-MoS₂ mixed lubricant (20% content) to compensate for its higher wear rate.
III. Typical Equipment Selection Cases in Ships
1. Ship Rudder Steering Gear Bearings
l Operating Condition: Periodic oscillating loads (15-25 MPa), salt fog erosion, frequent vibrations.
l Selection: High-strength brass (ZCuZn25Al6Fe3Mn3), ultimate pressure 50 MPa, salt spray lifespan 720 hours.
l Result: After a 100,000-ton bulk carrier switched to high-strength brass bearings, there was no corrosion or seizing within 5 years, and maintenance costs were reduced by 62%.
2. Seawater Pump Bearings
l Operating Condition: Continuous high speed (1500 rpm), direct seawater impingement, fretting wear.
l Selection: Aluminum bronze (ZCuAl10Fe3) with 15% fluorinated graphite embedded, improving corrosion resistance by 30%.
l Data: Wear rate reduced from 1.5×10⁻⁴ to 0.8×10⁻⁴, and lifespan extended to 6 years.
IV. Selection Decision Flowchart
1. Determine Equipment Type:
Deck Machinery (high load, salt fog) → High-Strength Brass
Propulsion System (high temperature, vibration) → Aluminum Bronze
Submersible/Special Equipment (extreme corrosion resistance) → Stainless Steel-Based Composite
2. Verify Lubrication Requirements:
Maintenance-Free Period >5 Years? → Stainless Steel-Based Composite (25% lubricant content)
Routine Maintenance (3-5 Years) → High-Strength Brass or Aluminum Bronze
3. Cost Constraints:
Budget Limited → High-Strength Brass (best cost-effectiveness)
High Value-Added Equipment → Stainless Steel-Based Composite (low lifecycle cost)
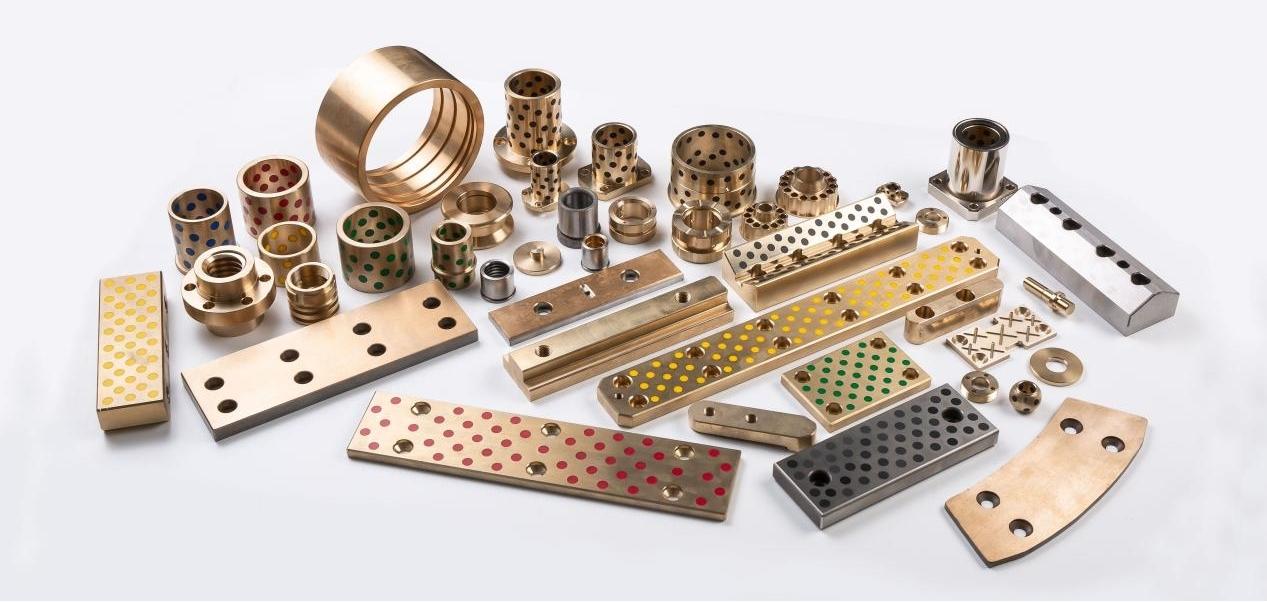
The selection of self-lubricating bearings for ships should adhere to the three principles of "prioritizing corrosion resistance, emphasizing load-bearing capacity, and focusing on lubrication":
l High-strength brass covers 80% of ship scenarios with balanced performance and is the cost-effective choice.
l Aluminum bronze secures key positions in propulsion systems with its high-temperature resistance and corrosion resistance.
l Stainless steel-based composites provide ultimate protection for deep-sea equipment.
In the future, with the popularization of surface modification technologies for copper-based materials (such as laser cladding with Al₂O₃ coatings), the corrosion and wear resistance of ship bearings will further improve, driving the shipping industry towards safer and more low-carbon development.
For more technical exchanges or selection advice, please contact Zhejiang Mingxu Machinery Manufacturing Co., Ltd.: [email protected]
Contact Us