In the fast-paced world of automotive manufacturing, precision, durability, and efficiency are the name of the game. One of the most critical processes in creating vehicle parts is plastic injection molding—a method used to shape everything from dashboards to intricate engine components. At the heart of this process lies a hidden hero: the solid-lubricating bearing.
So why are these bearings so vital in the production of automotive parts?
1. No More Grease and Oil Hassles
Traditional bearings need regular lubrication, usually with oil or grease, to reduce friction and keep moving parts working smoothly. But imagine trying to pause a high-speed assembly line every time you needed to re-lubricate a bearing—it’s a costly and time-consuming process! Solid-lubricating bearings, on the other hand, are self-lubricating. They contain materials like graphite or PTFE (Teflon) that naturally reduce friction without needing constant upkeep. This keeps the plastic injection process moving smoothly without interruption.
2. Resistant to Gunk and Grime
Plastic injection molding can be a messy business. During the process, plastic residue, dust, and other particles can accumulate in the machinery. In systems that rely on liquid lubricants, these contaminants mix with the oil or grease, leading to clogging, wear, and eventual breakdown. Solid-lubricating bearings don’t have this problem. They form a protective layer that doesn’t trap dirt and debris, allowing them to keep working even in tough, dirty conditions.
3. Built for Heat and Pressure
Plastic injection molding isn’t a gentle process. It involves extreme temperatures and high pressures to shape the molten plastic. Liquid lubricants can break down under these intense conditions, leading to increased wear and tear. But solid-lubricating bearings are tough! They’re designed to withstand the heat and pressure, ensuring that the machinery keeps functioning smoothly without the lubricant breaking down or evaporating.
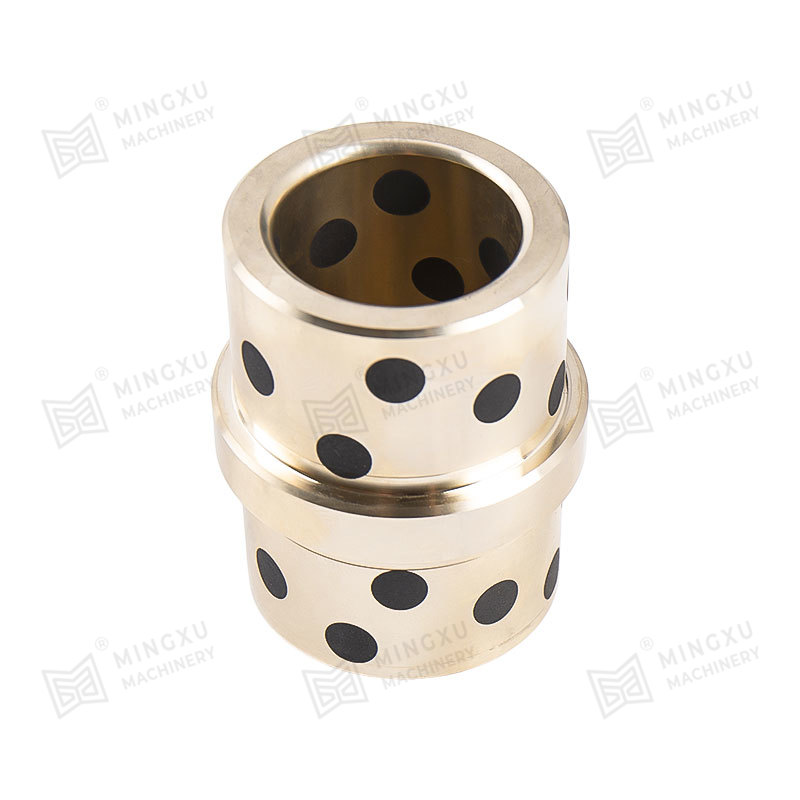
4. Less Maintenance, More Productivity
In an industry where time is money, frequent maintenance can be a significant drain on productivity. Solid-lubricating bearings need far less attention compared to traditional bearings. Since they don’t require constant re-lubrication, they allow machines to run longer without stopping for upkeep, which increases output and efficiency in the production line.
5. Precision is Key
Plastic parts in cars need to be exactly right—whether it’s a dashboard component or a gear housing. Solid-lubricating bearings help keep mold injection machines running with high precision. Their consistent, reliable performance ensures that molds move smoothly and stay aligned, leading to fewer defects in the final products.
6. Longer Lifespan
Because solid-lubricating bearings are more resistant to wear and contamination, they last longer than traditional lubricated bearings. This means fewer replacements and less downtime, contributing to a more efficient and cost-effective manufacturing process overall.
In short, solid-lubricating bearings help automotive manufacturers produce parts faster, more reliably, and with greater precision. They thrive in the harsh, high-pressure environment of plastic injection molding, delivering performance that traditional bearings simply can’t match. By eliminating the need for constant re-lubrication, they allow factories to focus on what they do best—building the cars of tomorrow!
Contact Us