As a high-performance self-lubricating bearing component, flanged graphite bronze bushings offer significant advantages in mechanical transmission, heavy-duty equipment, and harsh operating conditions such as high temperatures and dusty environments, thanks to their unique structural design and material properties. The flanged structure not only optimizes the load-bearing characteristics of traditional bearings but also enhances installation efficiency and system reliability through integrated design. They have become the preferred solution in fields such as construction machinery, metallurgical equipment, and shipbuilding. Below is an overview of their core advantages from a practical application perspective.
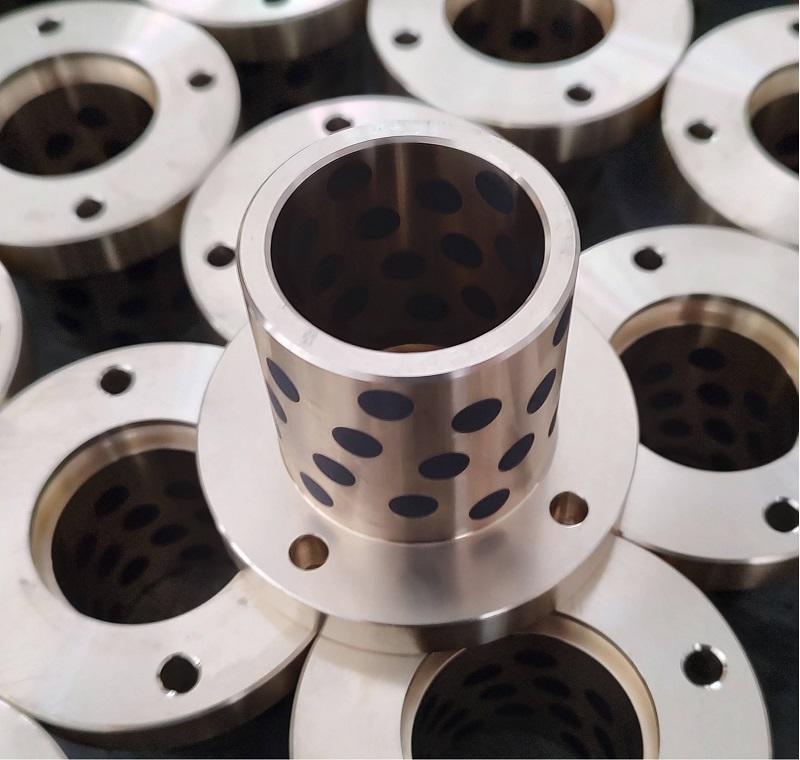
Core Application Advantages of Flanged Graphite Bronze Bushings
Integrated Axial Positioning Function
The flanged structure achieves axial self-locking through mechanical engagement between the flange edge and the mounting hole, effectively preventing axial displacement caused by vibration or load fluctuations during operation. This reduces the need for additional fasteners (such as retaining rings or end covers) and simplifies the assembly process.
Enhanced Composite Load-Bearing Capacity
The flanged design distributes combined radial and axial loads, excelling in scenarios involving oscillating or eccentric motions (e.g., articulated joints, connecting rods). It minimizes the risk of eccentric wear caused by lateral forces, thereby extending service life.
End-Face Protection and Wear Control
The flange covers the end-face contact area, preventing direct friction between the shaft shoulder and the bushing edge. Combined with the self-lubricating graphite layer, it significantly reduces end-face wear, making it suitable for frequent start-stop or low-speed, heavy-load applications.
Contamination Resistance and Lubrication Retention
The physical barrier formed by the flange prevents external dust and debris from infiltrating the friction pair while reducing lubricant leakage. This enhances reliability in dusty environments such as mining machinery and agricultural equipment.
High-Temperature and Low-Speed Adaptability
The graphite-embedded copper matrix design ensures stable lubricant release at high temperatures (up to 400°C). The flanged structure further prevents installation misalignment due to thermal expansion, making it suitable for applications like metallurgical rollers and high-temperature kilns.
Ease of Installation and Maintenance Cost Optimization
The flanged structure provides an intuitive installation reference, eliminating the need for precise axial position adjustments. This is particularly advantageous for mass assembly or rapid field repairs, reducing labor and time costs.
Lightweight Design and Space Efficiency
The integrated design reduces the need for auxiliary components, lowering overall weight and saving installation space. This is a significant advantage in industries like aerospace and new energy vehicles, where compactness is critical.
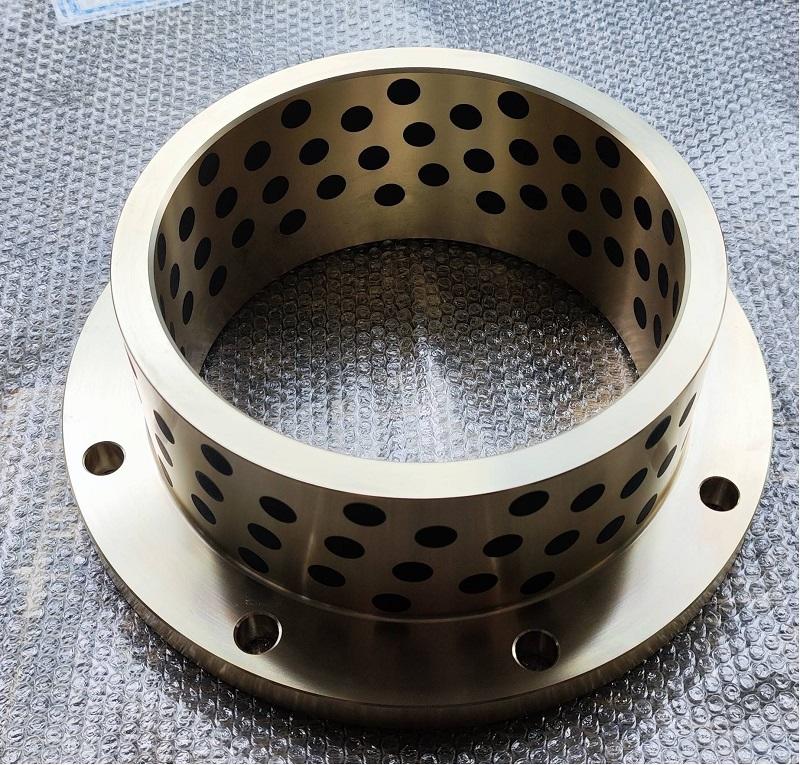
Typical Industry Applications (2020–2023)
l Construction Machinery: SANY excavator articulated arms equipped with flanged graphite bronze bushings achieved a 30% increase in service life and extended maintenance intervals to over 2,000 hours (data from Journal of Construction Machinery, 2022).
l Steel Metallurgy: After upgrading to flanged graphite bronze bushings, Baosteel's hot-rolling mill roller bearings reduced annual failure rates by 42% and withstood short-term high-temperature conditions up to 650°C (internal industry report).
l Shipbuilding: Jiangnan Shipyard applied these bushings to rudder swing mechanisms, enabling oil-free lubrication in seawater-corrosive environments and reducing marine pollution risks (2023 Maritime Exhibition case study).
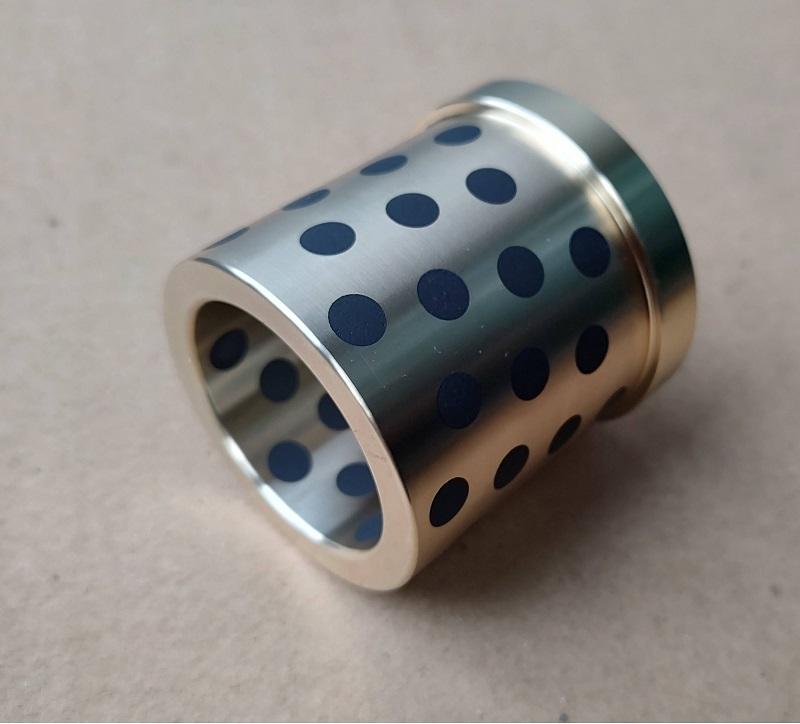
As a flagship product of Zhejiang Mingxu Machinery Manufacturing Co., Ltd., flanged graphite bronze bushings demonstrate exceptional practical value in dynamic load, complex environmental, and long-cycle operation scenarios through synergistic optimization of structural innovation and material performance. Their technological advantages have been validated through large-scale applications by leading industry enterprises, making them a key component for enhancing equipment reliability and reducing total lifecycle costs. In the future, with continuous upgrades in manufacturing processes, their application boundaries will further expand into emerging fields such as new energy and robotics. We sincerely hope to engage in deeper exchanges and collaborations with you regarding this product: [email protected].
Contact Us