The copper powder layer in the MXB-DUF SF-1F oil-free composite bearing is an essential intermediate layer that serves multiple key functions, primarily enhancing the bond between the steel plate base and the plastic top layer. This enhancement is critical because the composite bearing’s performance depends heavily on the integrity of these layered materials under various mechanical and environmental stresses.
1. Mechanical Interlocking and Adhesion Enhancement
The copper powder layer is typically applied to the steel plate using a sintering process, which results in a porous, textured metal surface. This porous structure is vital because it creates numerous microscopic voids, ridges, and cavities on the steel surface. When the plastic layer is applied—often through injection molding or lamination—the molten plastic is able to flow into these tiny pores and crevices, forming a strong mechanical interlock. This interlocking effect significantly improves adhesion because it is not solely dependent on chemical bonding, which can be weaker or susceptible to environmental degradation.
Unlike a smooth metal surface that relies mainly on surface energy for adhesion, the porous copper powder layer provides a physical anchor for the plastic, helping to resist delamination caused by shear forces, vibrations, or thermal cycling during operation. This mechanical bonding is crucial in applications where the bearing is exposed to repetitive loads or continuous motion.
2. Thermal Expansion Compatibility and Stress Reduction
Different materials expand and contract at different rates when subjected to temperature changes, a phenomenon described by their thermal expansion coefficients. Steel has a relatively low thermal expansion rate compared to plastics, which generally expand more when heated. This mismatch can induce stresses at the interface between the steel plate and the plastic layer, potentially leading to cracks, warping, or separation over time.
The copper powder layer acts as an intermediary “buffer” with thermal expansion characteristics that fall between those of steel and plastic. This gradation helps to absorb and reduce the stresses caused by temperature fluctuations, maintaining the structural integrity of the bond. By mitigating thermal stresses, the copper powder layer prevents micro-cracking and premature failure, thereby extending the operational life of the bearing, especially in environments with high or variable temperatures.
3. Friction Reduction and Wear Mitigation
Beyond bonding, the copper powder layer also contributes to the bearing’s frictional properties. Copper is known for its relatively low coefficient of friction and good lubricity compared to many other metals. This characteristic helps reduce frictional heat and wear at the interface between the steel substrate and the plastic overlay during operation.
By minimizing friction where the steel plate and plastic layer meet, the copper powder layer not only preserves the bond but also contributes to the overall wear resistance of the composite bearing. This lubricating effect complements the self-lubricating nature of the plastic layer, allowing the bearing to maintain smooth operation over long periods without external lubrication.
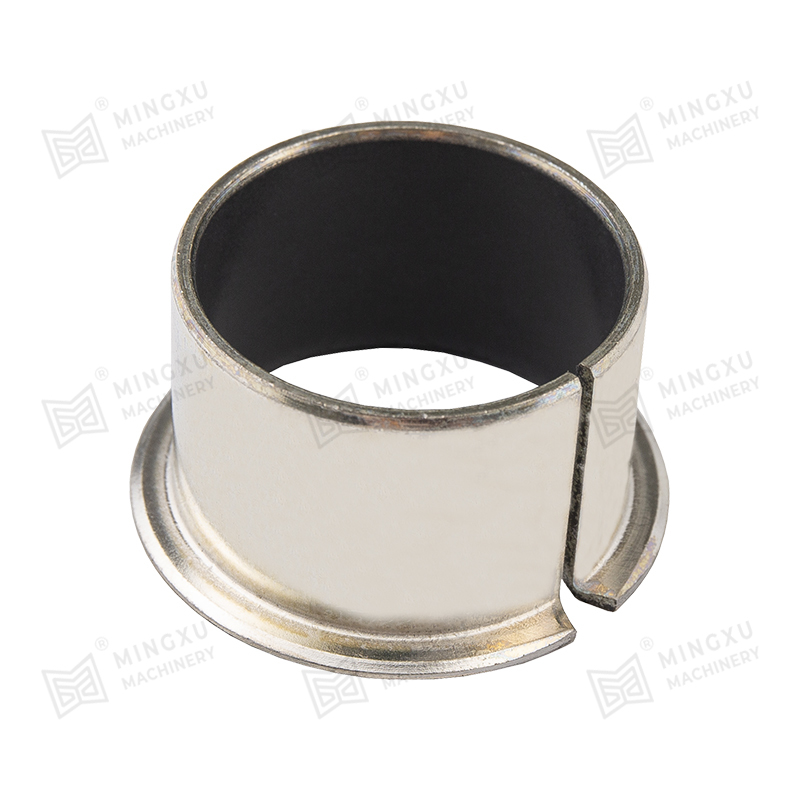
4. Load Distribution and Structural Reinforcement
The copper powder layer also plays a structural role by distributing mechanical loads more evenly across the interface. When the bearing is subjected to forces—whether compressive loads, shear forces, or impacts—the copper powder layer helps spread these stresses uniformly, reducing localized stress concentrations that could otherwise cause deformation or failure at the bonding interface.
This load-distribution function is particularly important for flange bearings like the MXB-DUF SF-1F, which often operate under heavy load and in conditions where precise support and stability are required. The copper powder layer’s ability to evenly transmit forces enhances the bearing’s durability and reliability.
In summary, the copper powder layer in the MXB-DUF SF-1F bushing enhances the bonding between the steel plate and plastic layers through several synergistic mechanisms:
-
It provides a porous, textured surface for the plastic layer to mechanically interlock with, significantly improving adhesion beyond chemical bonding alone.
-
It acts as a thermal buffer, reducing stresses caused by differences in thermal expansion between metal and plastic layers.
-
It contributes to friction reduction and wear resistance by leveraging copper’s natural lubricity, thereby protecting the interface during operation.
-
It distributes mechanical loads evenly across the bond, preventing stress concentrations and improving the bearing’s structural stability under heavy loads.
These combined effects ensure the MXB-DUF SF-1F bushing maintains its structural integrity, low friction, and long service life even in demanding industrial environments where temperature fluctuations, heavy loads, and continuous motion are common.
Contact Us